Optimal Design Studies for Occlusion Devices
The human heart has four chambers which are separated into two superior atria and two inferior ventricles. The wall tissue of the human heart called septum which separates the chamber of the heart, one of the septa gets defected is known as a septal defect. It is classified into two types based on the location, if it is in the upper chamber of the heart known as Atrial Septum Defect (ASD) whereas in the lower chamber is known as Ventricular Septum Defect (VSD). ASD/VSD is nothing but a hole or opening between upper/lower chambers of the heart to allow blood to flow around the lungs. This defect is treated by using occlusion devices. The following devices are the commonly available devices:
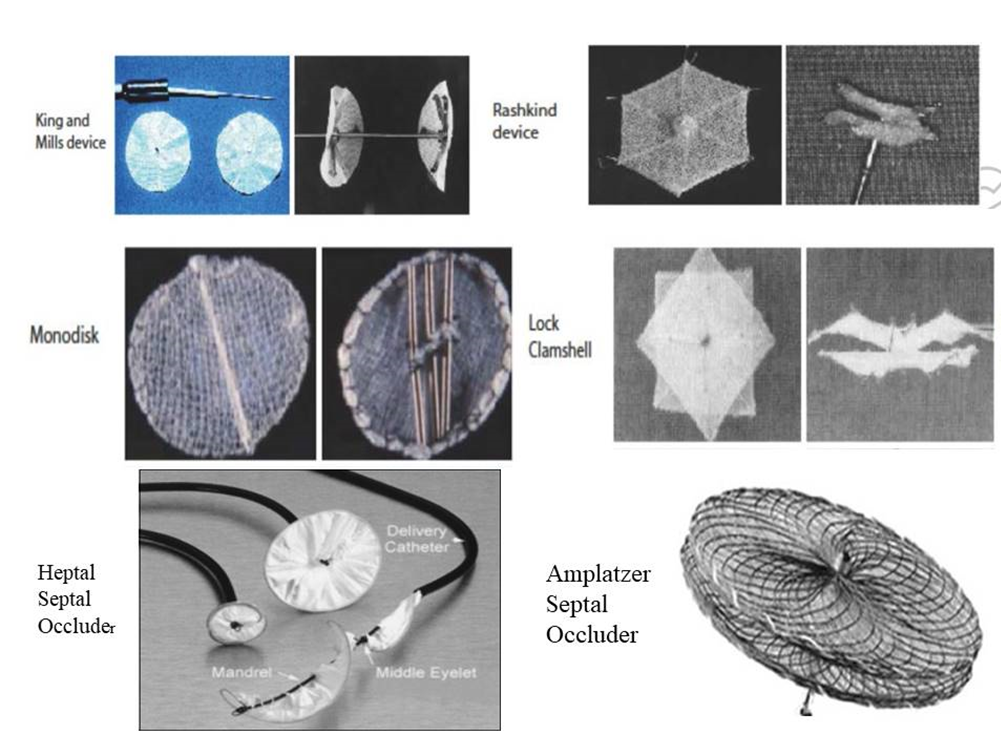
The objective of our research group is to develop an optimal design, by using the Finite Element Method by ANSYS software and validate the obtained data with experimental data of available journals. After the deployment of the occlusion devices, they might cause problems of embolization, erosion of these devices, impingement of devices, hemolysis etc., The concept of bio-resorbable evolved to address these problems, this device itself may be degradable once the defect is closed and it gets dissolved into the body. The new research area called wear upon tissue due to contact by devices in relative motion needed to make wear model. This information provides to do better design, impacts of devices upon living tissue, and able to choose the best material. The Wear analysis will be done to predict the loss of material and lifetime of the device.
Balloon Bursting studies
Balloons are used in the field of balloon valvuloplasty, placing stents inside the blood vessel or aortic valves. We are interested to find out the critical bursting pressure of a balloon. If the balloon gets burst upon the tissue, the balloon will be attached with it and difficult to remove from the bursting site. This study is processing by using ANSYS software, Explicit dynamics tool. We were already done by using polyurethane material. The bursting for different thickness was shown below.
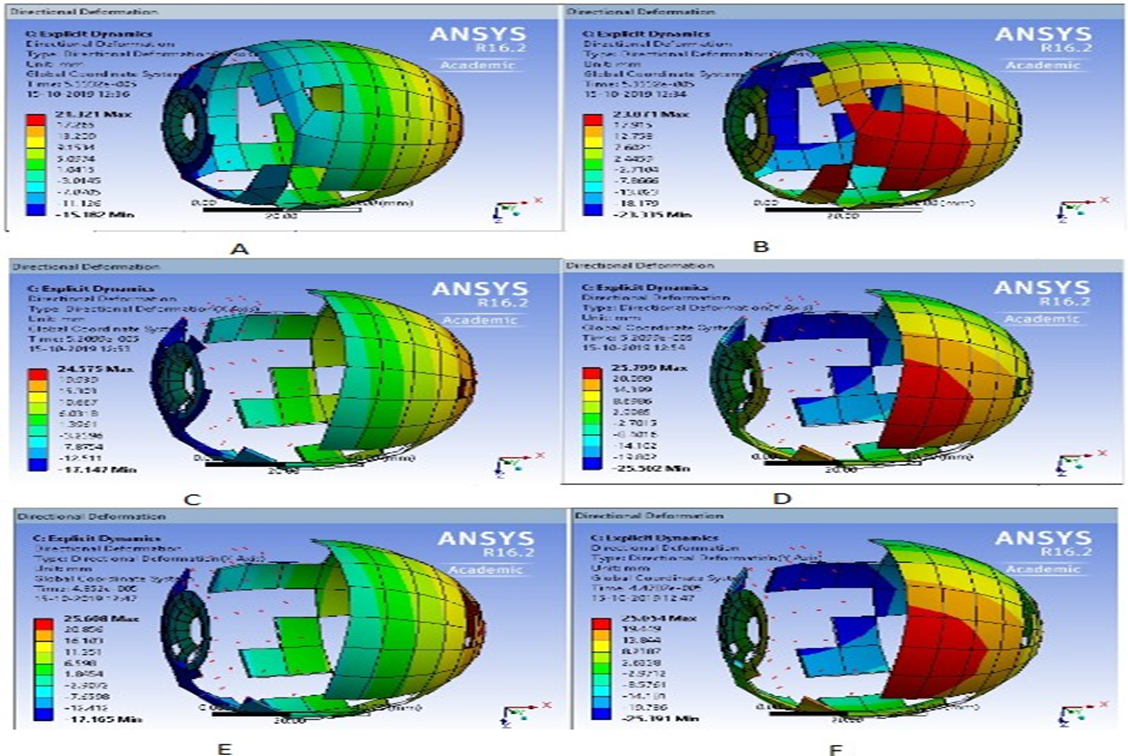
In general, the elastomers are used as material for balloons. The elastomers are hyper-elastic materials, this material is highly deformable, nonlinear stress and strain curve. They are different hyper-elastic models are available. So the selection of these materials depends on material and load. The models are Polynomial, Mooney-Rivlin, Neo-Hookean, Yeoh, Ogden, Arruda-Boyce, etc., the best model will be chosen by the technique least square curve fitting of experimental data of uniaxial, biaxial and planar or shear test of stress and strain curve. The ANSYS software would be used for these studies, to choose the best appropriate model and to find out critical bursting pressure for a particular thickness of the balloon.
References:
- Sonetha, V.A. and Bellare, J.R., 2014. Flow simulation of cardiac defects to evaluate effectiveness of occlusion devices. Journal of Medical Devices, 8(2).
- Sonetha, V.A. and Bellare, J.R., 2015. Simulation of pulsatile blood flow through various cardiac defects and quantitative measurements of shunted blood volume. Procedia Materials Science, 10, pp.706-713.
- Sonetha, V.A. and Bellare, J.R., 2016. Mathematical modeling and simulation of an occlusion device in a blood vessel. Cardiovascular Engineering and Technology, 7(4), pp.420-431.